Black Hawk Parts Fundamentals Explained
Wiki Article
Not known Details About Black Hawk Parts
Table of ContentsSee This Report about Black Hawk PartsMore About Black Hawk PartsThe Best Strategy To Use For Black Hawk PartsWhat Does Black Hawk Parts Do?
KAMAN K-1200 K-Max synchropter In a side by side blades configuration, 2 horizontal, counter-rotating rotors are installed side-by-side on a helicopter (or transverse rotorcraft). black hawk parts. The anti-torque effect is given by the opposing rotation of the two primary blades. The side-by-side setup is just one of the feasible trip configurations of a tilt-rotor aircraft, when the rotors remain in the vertical placement to supply upright lift.It is essential that components are created and completed in a right fashion. As a helicopter spare parts dinner in the United States, Jones Metal Products is right here to create and complete helicopter components in a precise and prompt fashion. Jones Steel Products has over 95 years in the hydroforming industry, a process that we make use of for a variety of parts in the aerospace and protection sectors.
As a helicopter parts distributor, Jones Metal Products constantly welcomes outdoors organizations in for correct accreditations. These outside organizations observe as well as verify the different procedures that we carry offer where we are making continuous advances in composite manufacturing of helicopter parts. ISO 9001:2015 without Style This accreditation ties to our high quality administration system.
When it becomes a trusted as well as valued helicopter parts maker, making breakthroughs in composite manufacturing of helicopter parts features the area. The procedures via which we manufacture helicopter components are always being surpassed by our competent group. Our group of engineers, designers, and metalworkers have been innovating our services because the 1920s.
Little Known Questions About Black Hawk Parts.
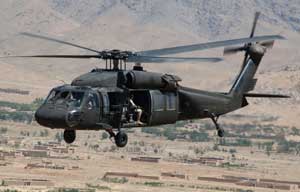
They can also assist you to recreate older helicopter components that originate from discontinued runs all while restraining with our high requirements of quality and regular manufacturing. Hydroforming, Rubber pad forming, Warmth treating, Stretch creating As a top helicopter parts manufacturer, Jones Metal Products enjoys to collaborate with clients in the aerospace, defense, and also airplane industries.
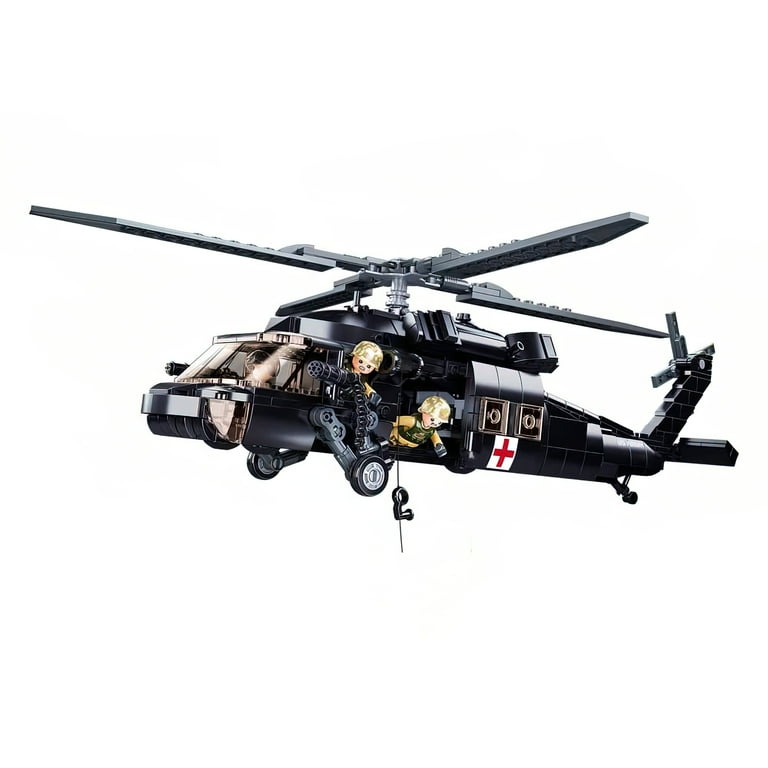
Helicopters are identified as rotary wing airplane, and also their rotary wing is commonly referred to as the major rotor or merely the blades. Unlike the more usual fixed wing airplane such as a sport biplane or an airplane, the helicopter is capable of straight upright take-off and also landing; it can additionally float in a fixed setting.
The autogiro he subsequently developed bundled functions of both the helicopter and also the airplane, although it looked like the last more. The autogiro had a rotor that worked something like a windmill. When instated by cabbing on the ground, the rotor might create extra lift; however, the autogiro was powered mainly by a standard airplane engine.
Some Known Details About Black Hawk Parts
To steer a helicopter, the pilot must adjust the pitch of the blades, which can be set 3 ways. In the collective system, the pitch of all the blades connected to the blades equals; in the cyclic system, the pitch of each blade is made to fluctuate as the rotor rotates, and also the 3rd system utilizes a mix of the very first two.A related issue occurs due to the fact that, as the helicopter moves onward, the lift underneath the blades that enter the airstream first is high, yet that under the blades on the contrary side of the rotor is low. The net result pop over to these guys of these troubles is to undercut the helicopter. Normally, the ways of making up for these uncertain variants in lift and drag is to manufacture adaptable blades attached to the blades by a hinge.
Torque, one more trouble related to the physics of a revolving wing, causes the helicopter body (cabin) to turn in the opposite instructions from the Recommended Reading rotor, especially when the helicopter is relocating at low rates or hovering. To counter this reaction, many helicopters utilize a tail rotor, a revealed blade or ducted fan placed on completion of the tail boom generally seen on these craft.
He tried out for more than twenty years as well as finally, in 1939, flew his first flight in a craft referred to as the VS 300. Tethered to the ground with long ropes, his craft flew no more than 50 feet off the ground on its initial a number of trips. Even then, there were problems: the craft flew up, down, and sideways, yet not forward.
Black Hawk Parts - Truths
and asked to try one of their brand-new major structure office computers. By 1951, Parsons was trying out having the computer system's calculations really assist the equipment device. His suggestions were inevitably become the computer-numerical-control (CNC) maker device market that has changed modern-day manufacturing methods. Read Full Article 1 Each specific tubular component is reduced by a tube reducing maker that can be swiftly readied to generate various, exact sizes and specified batch quantities.For apart from small bends, tubes are full of molten salt silicate that solidifies as well as gets rid of kinking by causing television to flex as a solid bar. The supposed water glass is after that removed by putting thebent tube in boiling water, which melts the internal product. Tubing that must be bent to match body shapes is fitted over a stretch forming machine, which extends the metal to a specifically contoured shape.
The last process requires infusing wax or an alloy with a low melting factor into a mold and mildew or pass away. When the template has actually been formed, it is dipped in molten steel as lot of times as needed to attain the thickness wanted. When the part has actually dried, it is warmed to make sure that the wax or alloy will thaw as well as can be poured out - black hawk parts.
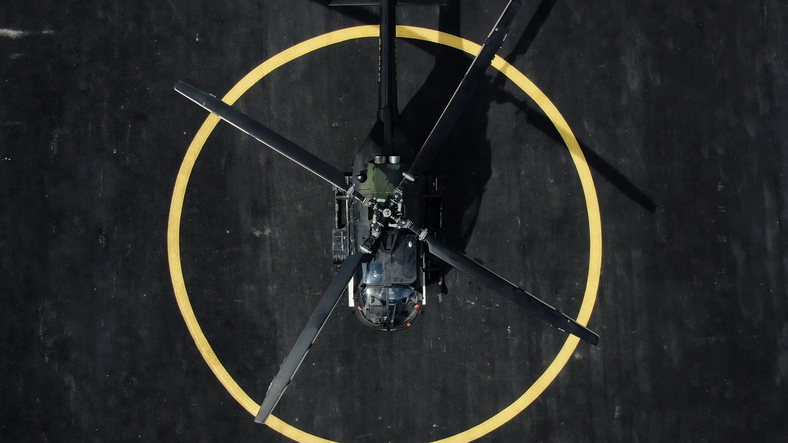
Report this wiki page